A robotic solution for repetitive pick & place tasks
Automating repetitive pick & place tasks (such as palletizing) is one of the main applications for collaborative robots — and for good reason. The robots are able to perform repetitive tasks precisely around the clock and in tight spaces. Relieve your employees and talk to one of our robotics experts today about the costs and feasibility of your processes.
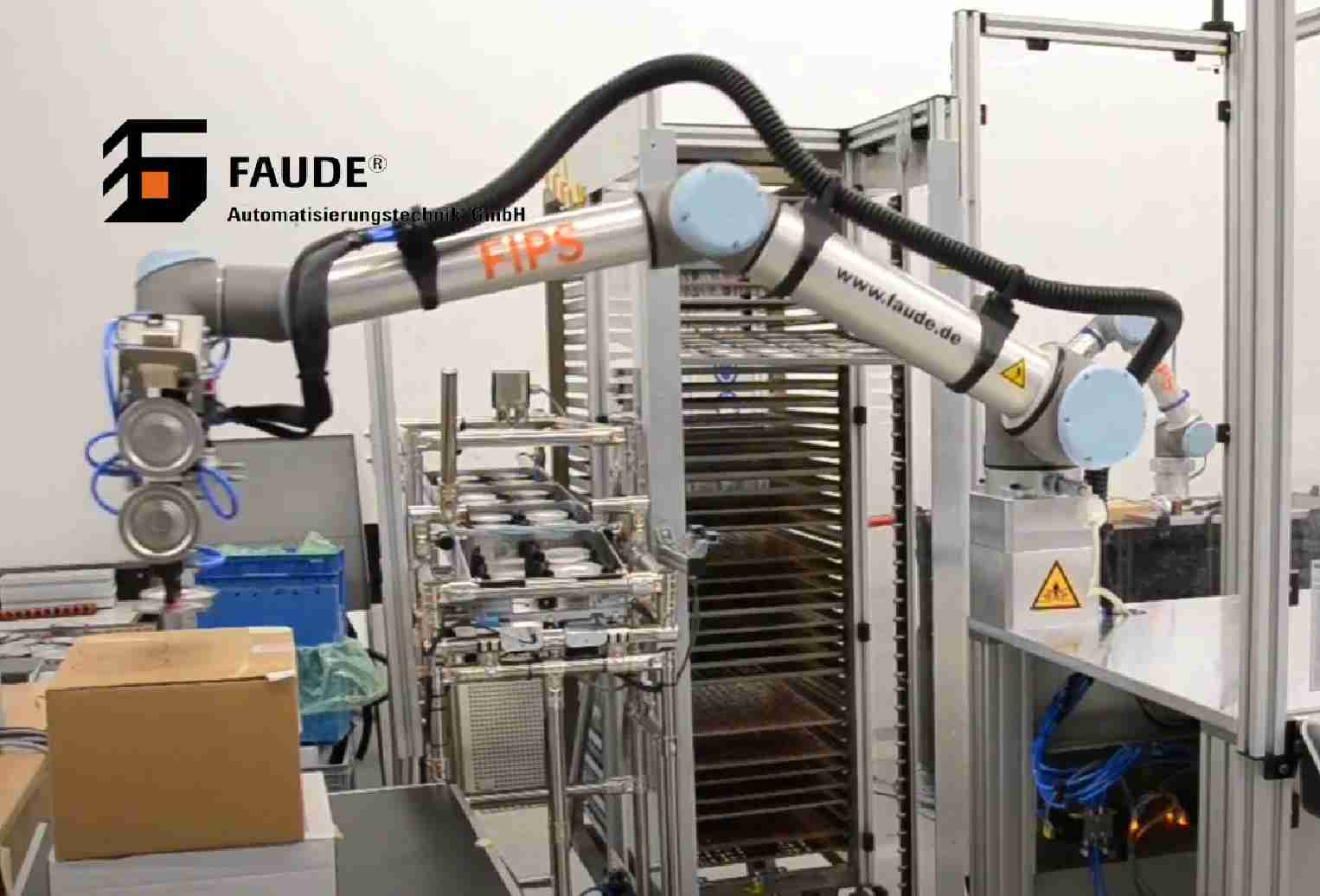
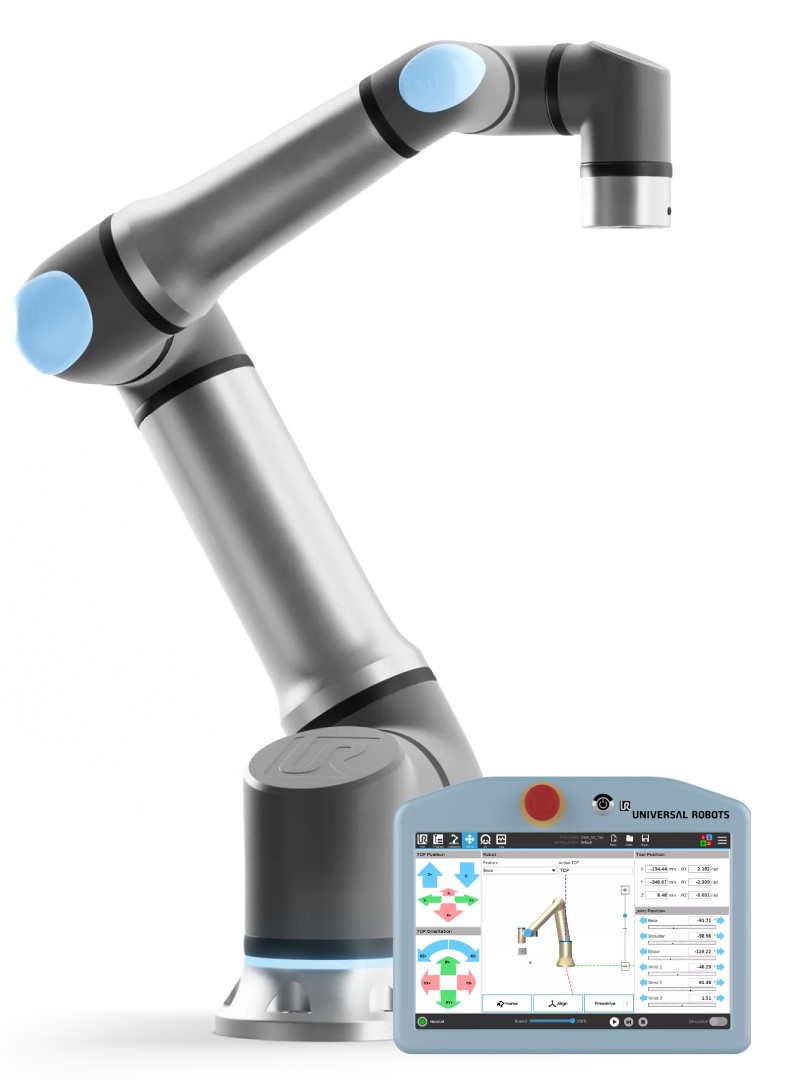
For workpieces up to 25 kg, cobots are the right choice
Thanks to integrated collision detection, cobots can share the work space with humans even without a protective cage, which enables efficient collaboration in confined spaces. However, for reasons of occupational safety, the robots are limited to a maximum payload of 30 kg, which must be sufficient for the workpiece and end effector (UR30 is the strongest cobot available). One of the main reasons why cobots are still often preferred over classic industrial robots is their very easy operation via teach counterparts with an intuitive graphical user interface and lead-through programming functions. Programming Pick & Place according to defined patterns, such as palletizing, is therefore no problem.
The right tooling for every process
For the various workpieces, whether simple boxes, KLTs, buckets, bags or others, there are suitable end-of-arm tooling options such as vacuum, electric or pneumatic grippers. Often, a customer-specific tool can also be developed if standard grippers do not work. In pick & place applications such as palletizing, it is particularly important to consider occupational safety at an early stage, as the workpieces can be heavy and edgy. Our solutions usually use light curtains (robot stops), area scanners (robot slows down) or protective grids (physical separation of the work area).
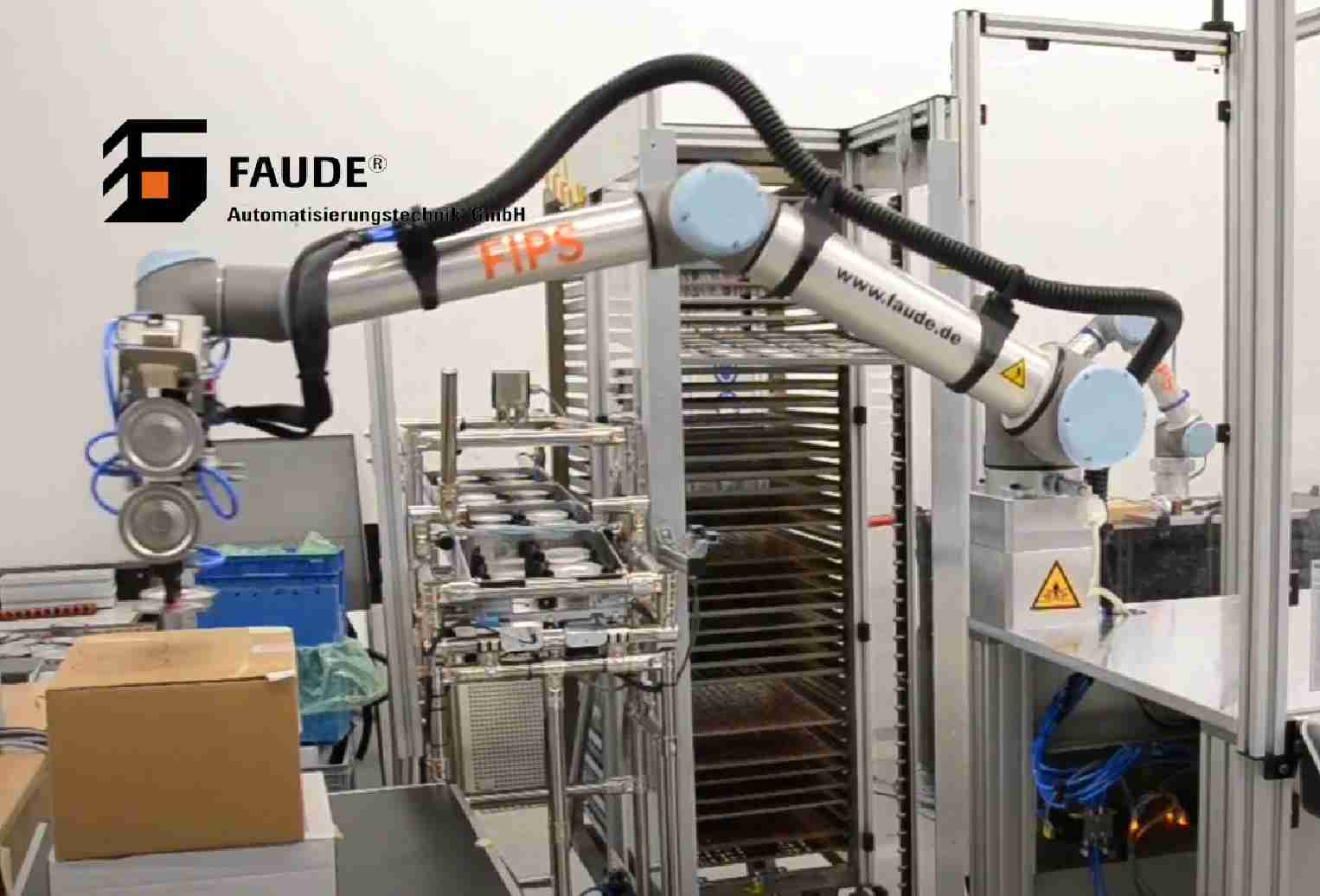
A sample application using Universal Robots
A short video of an application we have implemented for automated loading of a dispenser with a UR cobot. Another pick & place example, which we created with a custom-made gripper, can be found here.
Your benefits at a glance
Pick & place by pattern
The robot can pick up and drop workpieces at defined positions, according to defined patterns, or even chaotically (bin picking).
Suitable tools
Whether vacuum, electric, pneumatic or special grippers, there is a suitable gripper for most workpieces.
Appropriate safety concept
Whether it's an area scanner, a light barrier or a protective cage, depending on the pick & place process, we find a safe solution.
Collaborative
Thanks to integrated collision detection, the robot can work closely with humans even without a protective cage.
Space-saving
The robot weighs only around 40 kg, has a very small footprint and no bulky protective cage, which saves valuable space.
Mobile base
Installing the robot on a mobile base makes the application even more flexible.
CE documentation
Each of our robotic solutions comes with detailed risk assessment and CE documentation to ensure a safe working environment.
Easy operation
Thanks to the intuitive graphical user interface, even employees without programming knowledge can quickly set up new processes.
Flexible
The ease of use of the application also enables rapid adaptation to new processes should requirements change in the future.
The next steps to your robotic solution
In just five steps and a few weeks, we will guide you to your individual automation.
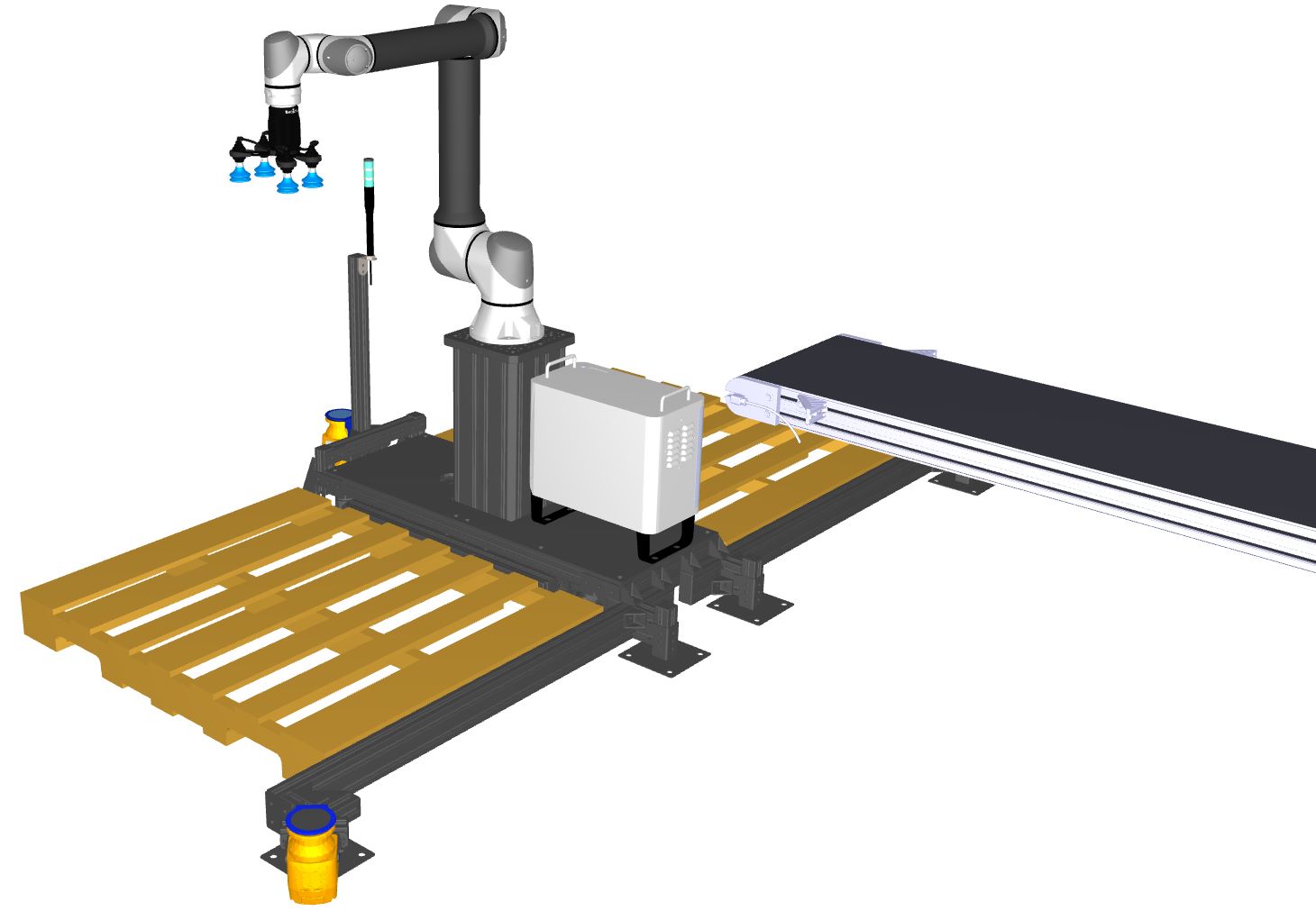
A short initial conversation to get to know each other, define the requirements, estimate feasibility and costs.
Once we have discussed your solution and a collaboration appears useful, we will arrange a non-binding appointment with you on site. We visit your production, check the conditions and create a final concept.
As soon as the concept is ready, we will prepare a binding offer. We are also happy to prepare a profitability calculation.
We build the plant according to your requirements in our production. Depending on the project, this usually takes 4 to 8 weeks.
We deliver the system (as far as possible) on a turnkey basis to minimize downtime. You can then use the power of the robotic solution around the clock!
Let's automate effectively together
We are a system integrator with more than 30 years of experience in automation technology. Benefit from our know-how from hundreds of projects and make your automation a success faster!
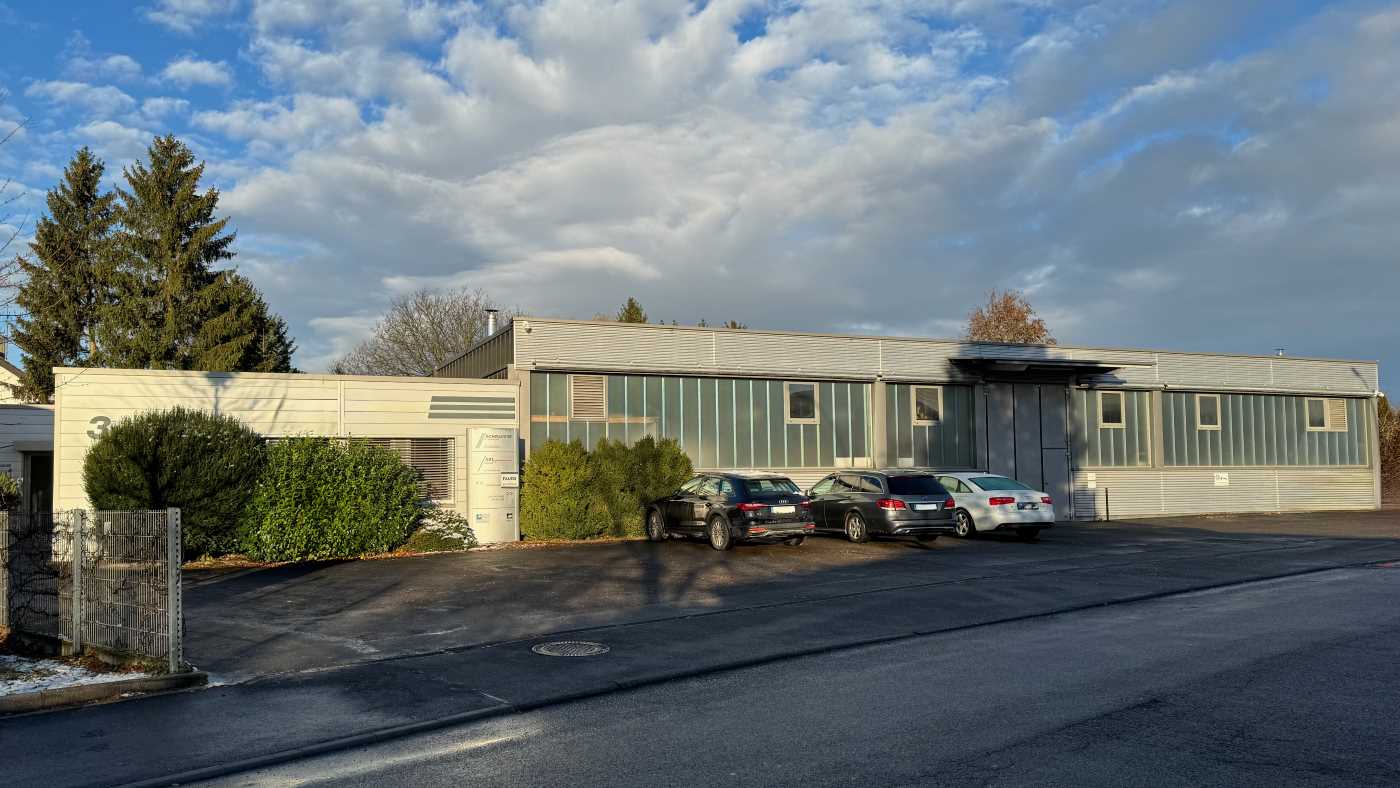